Breton XpressTop is the single most advanced management software designed specifically around improving the kitchen top production cycle.
XpressTop increases your productivity, while reducing costs to give your fabshop the competitive edge it needs.
This intuitive solution is defined by a modular approach, leading you through each stage of production: from sales, to design, passing through inventory all the way through delivery.
Each module seamlessly integrating and communicating with the next, increasing efficiency at every stage of production.
XpressTop increases your productivity, while reducing costs to give your fabshop the competitive edge it needs.
This intuitive solution is defined by a modular approach, leading you through each stage of production: from sales, to design, passing through inventory all the way through delivery.
Each module seamlessly integrating and communicating with the next, increasing efficiency at every stage of production.
XpressTop WILL HELP YOU…
- INCREASES ACCURACY with the automatic generation of a mistake-proof Bill of Materials
- AUTOMATES THE ENTIRE PROCESS, expediting your sales and production cycle
- TRACKS ORDERS throughout each stage of production, granting you total transparency on the status of every project your shop is working on.
- SCHEDULES THE SELECTION & PURCHASE OF RAW MATERIALS in accordance with established delivery dates.
- SAVING RESOURCES through extremely efficient process management.
- ELIMINATES THE NEED FOR EXPENSIVE SPECIALIZED PERSONNEL By flawlessly managing and communicating between each stage of production unto completion without the restraints of human error and related costs.
- PRIORITIZES ORDERS AND SCHEDULING that may affect the timely production.
The INVENTORY module performs real-time tracking of your entire shops inventory, starting at the very beginning with slab purchasing orders and raw material management.
The INVENTORY module provides:
The INVENTORY module provides:
- Live digital photo database with sizes and characteristics of your slabs, including vein imaging
- Warehouse inventory management complete with material tracking within specific warehouse areas
- Tracking of all materials, coming from suppliers and going to clients
- Managing of all orders to raw material suppliers
- Automatic and easy issuing of purchase documents, such as quote requests, purchase orders, transport documents etc.
- Creation and control of slab remnants
- Inventory reports and statistics (material handling, purchase orders and invoices)
- Mobile device integration; making warehouse management possible out on the floor
- Management of raw material purchase prices
- Ability to commit material to sales, production, or site transfers when applicable
- Manage the reorder point of your inventory avoiding eventual downtime during the production process
- Quality control over purchased materials and issue of non-compliance instances
SALES
The SALES module is to simplify and expedite the sales process through an integrated Customer Relationship Management tool (CRM) that automates quotes, production orders, and scheduling of activities.
The SALES module provides:
- An industry specific Customer Relationship Management tool (CRM) organizes customer database, delivery terms, email storage, and Issuing of sales documents: quotes, sales orders, invoices, etc.
- Sales reporting and statistics such as orders per month, sales prices, discounts, internal production costs, etc.
- Real-time visualization of the order status (in conjunction with the production module)
- Price list management
- Scheduling of different activities such as: measurements at the installation site, date of production start and end, shipment date, installation and even on-site technical assistance
- Convenient task assignments (technician for measurements, forwarding agent, technician for installation, etc.)
- Management of raw material suppliers and committing or issuing a slab purchase order together with the inventory module
The DESIGN module is tailor-made around the unique demands of your engineering department enabling limitless creativity with a state of art CAD interface, complete with an entire library of templates from which to build upon.
- Project drawing interface with:
- CAD functions
- parametric shapes library
- DXF file import capability
- The capability to input project details, such as edge shaping, finishing, and even accessory types, etc.
- Quotes in collaboration with the sales module based on a specific drawing
- A complete list entailing project specifications and all materials necessary
- Easy exporting of the project in DXF format
- Archive management of finished projects in DXF files- both internally produced, or provided by your customers
- Seamless integration between the Design and Inventory modules facilitating management of raw material suppliers, and when needed, generating slab purchase orders
PRODUCTION
The PRODUCTION module is a tool that allows you to program, schedule and monitor all the different steps of your project.From the “production sheet” it is possible to trace the raw materials and all the components utilized, monitoring in real-time the actual status of human resources, providing to the machine operators all the scheduling activities to be performed.
Also allow to monitor and trace the status of the all pieces (finished or not) and the machine operator activities in order to minimize mistakes.
The PRODUCTION module provides:
- Scheduling of production phases and forecasting the time needed to realize a project
- Monitoring and tracking of each order phase (cutting, contouring, edging, finishing, packing, etc.)
- Real-time production reports and statistics, including, the final number of processed orders, processing times, production costs, etc.
- Sorting of material requests to their respective warehouses: slabs, remnants, pieces (in collaboration with the inventory module)
- Automatic transferring of working programs to Breton machines
- Analysis or different options in order to realize each piece.
- Checks for remnants or broken pieces to plan their reintegration into the production cycle
Breton conducts an active hotline service performed by highly specialized technicians. It is also possible to carry out technical service directly on the machine installed on the customer side without the physical presence of the machine operator.
Through the software for the remote assistance it is possible to perform remote monitoring and diagnostics by being connected directly to the customer machine in a safe and secure way.
Through hotline service it will be possible to solve remotely many eventual problems promptly, granting you enormous savings.
Through the software for the remote assistance it is possible to perform remote monitoring and diagnostics by being connected directly to the customer machine in a safe and secure way.
Through hotline service it will be possible to solve remotely many eventual problems promptly, granting you enormous savings.
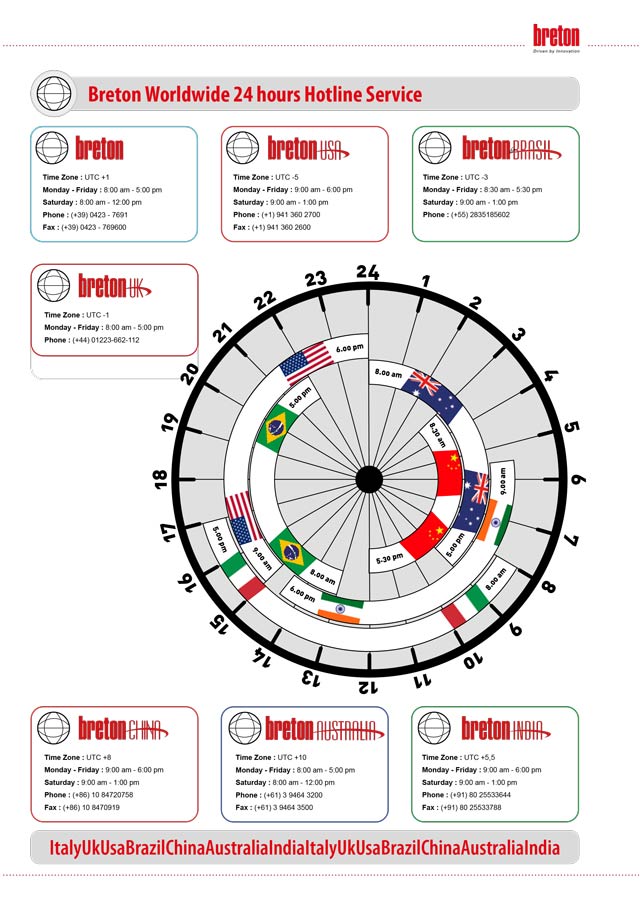
For more information and prices, on Breton XpressTop, contact mail@breton.it.
We’ll get back to you promptly.
Thank you for the attention and best regards.
Bye-bye
Sergio Prior
We’ll get back to you promptly.
Thank you for the attention and best regards.
Bye-bye
Sergio Prior